Surface Treatment Processes for Lifting Chains: How to Choose the Most Suitable Treatment
Lifting chains are widely used in various industrial fields, particularly in hoisting and lifting operations. Different surface treatment processes are commonly applied to improve the corrosion resistance, wear resistance, and service life of these chains.
How many surface treatments are available for lifting chains?
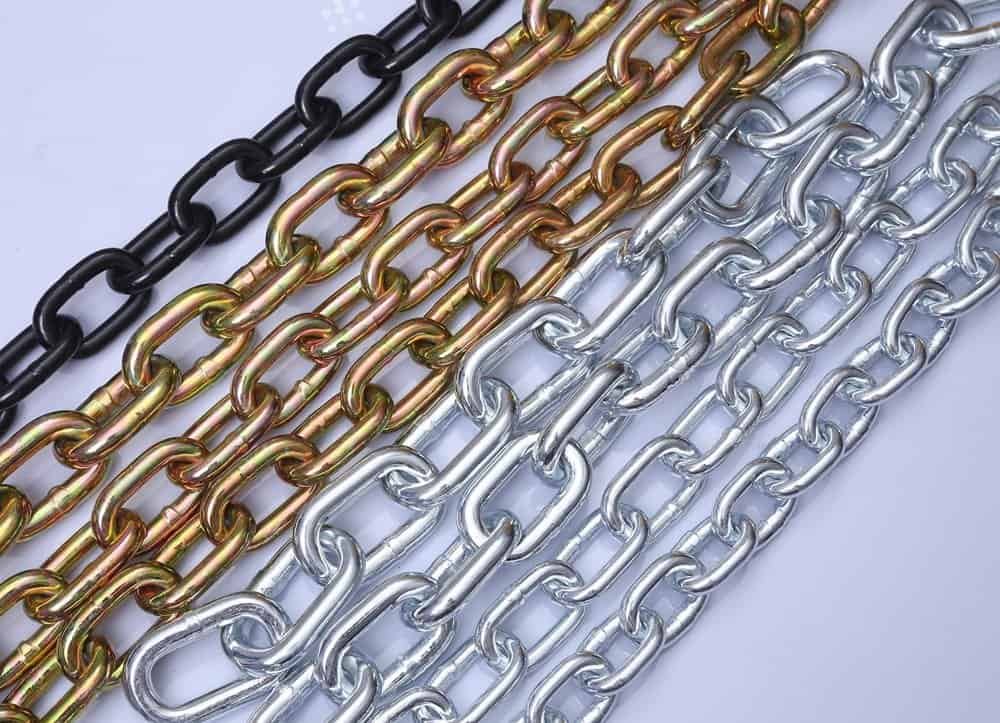
Each surface treatment process is briefly introduced below, highlighting its characteristics and comparing them with other methods. Using subheadings and short paragraphs helps improve readability.
- Galvanizing: Through galvanizing, a zinc layer will be formed on the surface of the chain, which can effectively prevent rust and corrosion and is suitable for outdoor or humid environments.
- Plastic spraying: The surface of the chain can be sprayed with plastic (such as polyethylene, polyurethane, etc.) to form a protective layer to increase wear resistance and have a better anti-corrosion function.
- Heat treatment: The chain is treated with high temperature to improve its strength and hardness and increase durability, especially in high-load applications.
- Painting: A layer of paint is applied to the surface of the chain, mainly to prevent rust, and also has a decorative effect on the appearance.
- Stainless steel: Stainless steel chains are suitable for environments with high corrosion resistance due to their inherent corrosion resistance.
- Phosphating: The surface of the chain is phosphate to improve the lubricity of the chain, reduce friction, and enhance corrosion resistance.
- Electroplating: A metal film is formed on the surface of the chain through electroplating technology to enhance its oxidation resistance and corrosion resistance.
- Black oxidation: A black oxide film is formed on the surface of the chain through chemical treatment to improve corrosion resistance and wear resistance.
How to Choose the Right Surface Treatment?
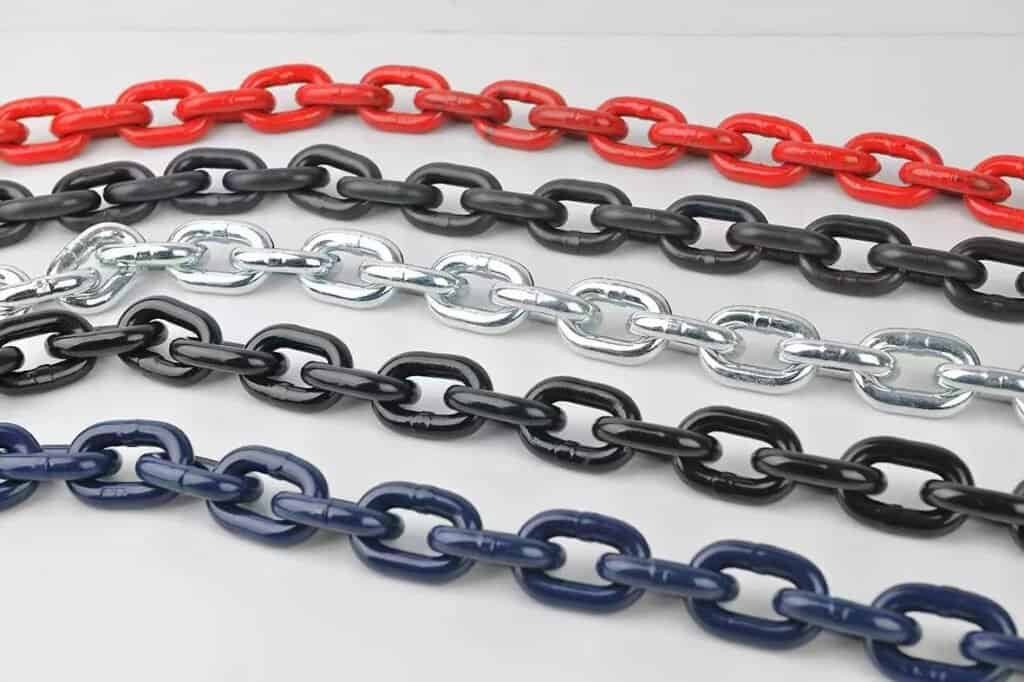
Choosing the right surface treatment for lifting chains is crucial to ensure their performance, durability, and longevity. Whether you’re in construction, logistics, or industrial operations, selecting the appropriate treatment can directly impact safety, maintenance costs, and operational efficiency.
- Environmental Conditions: If the chains are exposed to humid or highly corrosive environments, hot-dip galvanizing is the best option. For light corrosion environments, electro-galvanizing or spray coating may be more appropriate.
- Load Requirements: For heavy-duty applications, hot-dip galvanizing or spray-coated chains are recommended due to their superior corrosion resistance and surface strength.
- Aesthetic Requirements: If appearance is important, nickel-plated or electro-galvanized chains are more suitable for such applications.
Conclusion
In summary, choosing the right surface treatment process for lifting chains requires considering environmental conditions, load requirements, and aesthetic needs. Understanding the characteristics of each treatment process can help you make more informed decisions.