Common Stitching Defects in Lifting Slings and How to Spot Them
When it comes to lifting slings, most buyers focus on the webbing material, the label, or the load capacity. However, one often-overlooked yet critical component is the stitching. The stitching—specifically the sewing thread and pattern—plays a key role in the overall strength and durability of the sling.
Why Stitching Matters in Lifting Slings
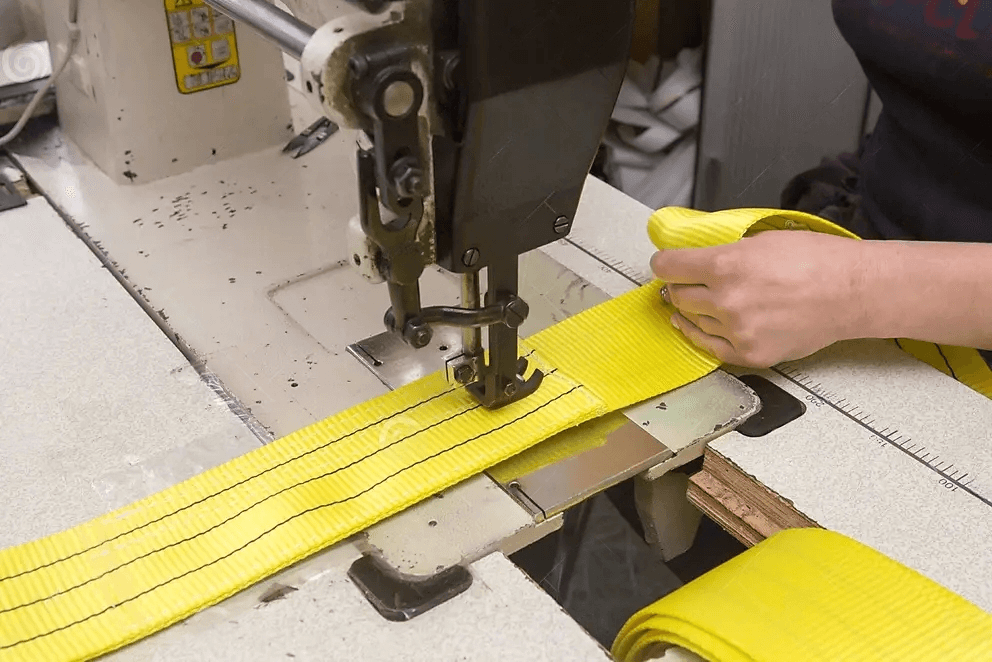
The strength of a lifting sling doesn’t come from the webbing alone—it relies heavily on the quality of stitching that holds everything together. Poor stitching can significantly reduce the Working Load Limit (WLL) and may lead to dangerous failures during lifting operations.
The stitching on a webbing sling isn’t just about holding layers together—it’s what keeps the sling strong and safe under load. If the stitching is poorly done, the entire sling becomes unreliable. Here’s what can go wrong:
- Lower Strength – Weak stitching reduces the sling’s working load limit (WLL), meaning it might fail when you least expect it.
- Safety Hazards – If stitches break under pressure, the sling can snap, risking injuries and damaging valuable equipment.
- Shorter Lifespan – Cheap stitching wears out faster, forcing you to replace slings more often.
Don’t cut corners on stitching—your safety and equipment depend on it. Always choose high-quality webbing slings with reinforced, durable stitching for maximum reliability.
What to Look for in Stitching Evaluation
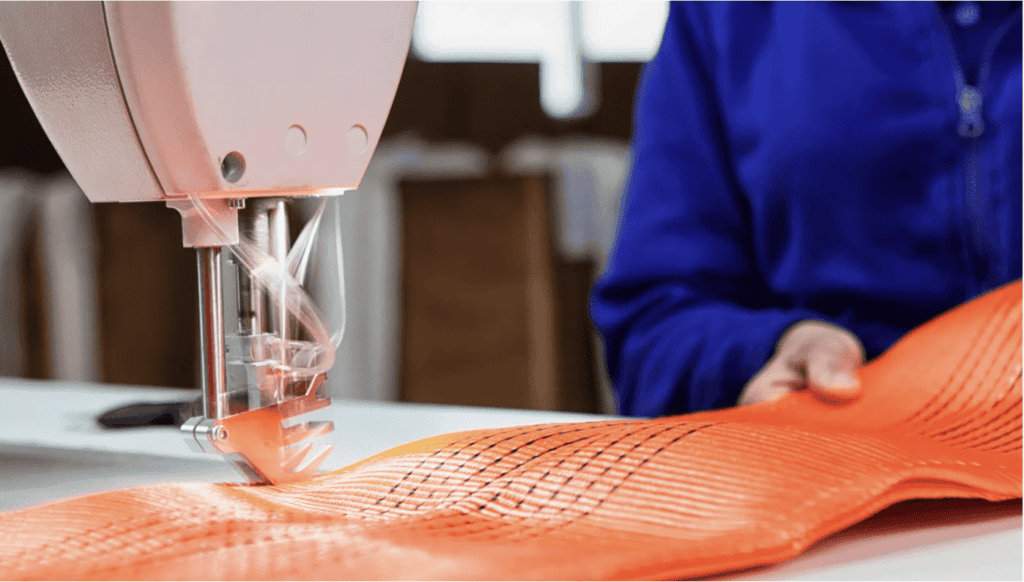
a. Thread Material
The type of thread used directly impacts performance:
- Polyester thread: Commonly used, good tensile strength and UV resistance.
- Nylon thread: Higher elasticity but weaker under wet conditions.
b. Stitch Pattern
Different stitch types provide different strength distributions:
- Zigzag or W-pattern: Balances flexibility and strength.
- Box stitch with cross (X-box): High-strength, used in heavy-duty slings.
- Multiple parallel lines: Common for standard-duty slings.
Make sure the stitch pattern is consistent, clean, and uniform across all slings.
c. Number of Stitches and Density
- More stitches per inch can enhance durability but may reduce flexibility.
- Uneven stitch lengths or skipped stitches are red flags for poor workmanship.
d. Visual Inspection Tips
- Are there any loose threads or skipped stitches?
- Are the stitch lines symmetrical and evenly spaced?
- Is the end of the thread sealed to prevent unraveling?
- Are loop areas double- or triple-stitched?
Stitching Quality and Its Impact on Sling Performance
The thread breaks under load—(lead to)—Complete sling failure
Inconsistent stitch pattern—(lead to)—-Weak points form under tension
Incorrect thread type–(lean to)—Reduced resistance to heat or chemicals
Skipped or loose stitches-(lead to)–shorter liftspan and reduced reliability
Important: The sling may look fine at first glance, but failure can occur suddenly under load if the stitching is not sound.
Frequently Asked Questions (FAQ)
Q: Can a webbing sling be re-stitched if the thread is damaged?
No. Once stitching fails, the sling’s structural integrity is compromised. Never re-stitch a damaged sling—always replace it to ensure safety.
Q: How does thread quality affect a webbing sling’s lifespan?
Cheap thread degrades faster from:
- UV exposure
- Abrasion
- Chemical exposure
High-quality polyester or nylon thread lasts longer, maintaining the sling’s strength over time.
Q: What’s the difference between hand-stitched and machine-stitched webbing slings?
- Machine stitching is more consistent and stronger, ideal for industrial use.
- Hand stitching may be used for repairs
Q: How often should I inspect stitching on webbing slings?
- Before every use – Quick visual check for damage.
- Regular inspections – Formal checks per standards (typically every 6-12 months).
Pro Tip: If you see any stitching issues, retire the sling immediately—safety comes first!
Conclusion
In lifting sling production, stitching quality is not a minor detail—it’s a core safety factor. Whether you’re sourcing webbing slings for construction, mining, or industrial lifting, don’t overlook the stitch—it holds everything together.